Grains Handling For Brewery
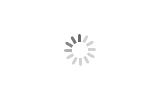
- HBET
- Shangdong, China
- Within 30days
- 50sets/month
Roll grinding flat, the material is easy to enter the grinding zone, convenient disassembly and repair; Gear transmission with fast and slow roll, high transmission efficiency, smooth running, low noise;
The self-aligning ball bearing roller,can guarantee the concentric rotary precision, can bear high speed and roller pressure; The high quality steel head, alloy steel rollers are dynamic balance, stable operation, long service life;
Fine rolling distance and the locking handle have the advantages of simple structure and convenient operation; Outer protective structure, simple and convenient; The machine has fully enclosed structure, safe and beautiful.
Grains handling for brewery
Main Application and usable range of Grains handling:
JMF series of malt crusher, is the latest product that is designed and developed by Shandong Academy Of Agricultural Machinery Science in the long-term basis of roller mill research, using advanced technology. The machine has the advantages of small size, high yield, reliable performance, energy saving, durable and convenient maintenance etc..
The equipment is mainly applicable to the production of beer malt and pharmaceutical, monosodium glutamate and other manufacturers. Also suitable for urban and rural small feed mill pulverizing forage use.
The use of environmental conditions
Crusher work site should be spacious, ventilation, and leave enough space and retreat with reliable fire extinguishing equipment.
Main structure and working principle of grains handling:
Main structure
Series of malt pulverizer are mainly composed by 1.feeder hopper 2.flow sheet adjustment mechanism 3.crushing chamber 4.roller gap adjustment handwheel 5.locknut 6.frame 7.discharging hopper 8.motor adjustment screw 9.motor 10.roller
Working principle
The raw unprocessed grains enter into the feeder hopper after removing impurities(such as stone,sand and metals etc, the water content no more than 12.5%). By the weight of raw grains and slight vibration of the machine, the raw grains enter into the space between two rollers,then being extruded and rolling grinded, the grinding down is discharged by discharging hopper.
Figure 1:schematic diagram for machine and adjustment mechanism
1.feeder hopper 2.flow sheet ajustment mechanism 3.crushing chamber 4.roller gap adjustment handwheel 5.locknut 6.frame 7.discharging hopper 8.motor adjustment screw 9.motor 10.roller
Grains handling Key performance indicators
Model performance indicator | JMF-1A | JMF-3A | JMF-5A | JMF-8A |
Productivity(take quality malt as example,the roller space 0.4-1.0mm) (kg/h per set) | 80-150 | 300-500 | 500-800 | 800-1000 |
Broken rate | user can adjust freely according to actual requirement | |||
Magnetic material content in grinding down(g/kg) | ≤0.003 | |||
Temperature of grinding down | ≤56 |
Grains handling Main technical parameters:
Model Data | JMF-1A | JMF-3A | JMF-5A | JMF-8A |
Outer size (L×W×H)(mm) | 700×620×1200 | 800×700×1600 | 800×800×1600 | 1150×700×1700 |
Weight(kg) | 120 | 150 | 180 | 550 |
Powder(kW) | 1.1 | 1.5 | 3 | 5.5 |
Fast Roller Spindle speed(r/min) | 700 | 700 | 700 | 800 |
Note: | 1.4-pole motor,the rotated speed is 1400r/min.2.The power should be configured appropriately,the speed of fast roller shouldn’t be improved at will. |